Stepping into the world of trading and investing can feel like entering an intricate maze. The charts, the numbers, the jargon it’s easy to feel overwhelmed. Yet, for those who take the time to truly understand the art of technical analysis, the maze slowly reveals a pattern, a rhythm, a story written in candlesticks and trendlines. This guide is crafted specifically for beginners stepping into 2025’s trading arena, to gently lead you through the complex yet fascinating strategies of technical analysis.
What makes 2025 unique? Why should you care about technical analysis now? And more importantly, how can you build a solid foundation that not only informs your trades but nurtures your confidence? These questions form the heartbeat of this journey.
Understanding the Soul of Technical Analysis.
Before diving into strategies, it’s crucial to connect with what technical analysis truly means. At its core, technical analysis is a way of reading market psychology through price movements. It’s not about predicting the future with certainty but about interpreting patterns, understanding momentum, and making educated decisions based on historical price behavior.
Imagine watching a bustling city from above. The crowd’s movement, traffic flow, the changing lights technical analysis is like observing these dynamic patterns but in the financial markets. It’s an ongoing dialogue between traders’ emotions: fear, greed, hope, and doubt, all reflected through price charts.
Unlike fundamental analysis, which dives into company financials or economic data, technical analysis is a language of price, volume, and time. It offers a visual representation of what traders collectively believe the value of an asset to be at any given moment. This is why it appeals to many beginners because it’s tangible, immediate, and often actionable.
Success is not a sudden destination but a continuous journey carved by perseverance, learning, and resilience. Each setback is not a failure but a stepping stone, teaching us invaluable lessons that refine our character and sharpen our vision. When you embrace the process with patience and an open heart, the obstacles transform into opportunities. Remember, it’s not the speed at which you travel but the commitment to keep moving forward that ultimately shapes your triumph.
Why Technical Analysis Matters.
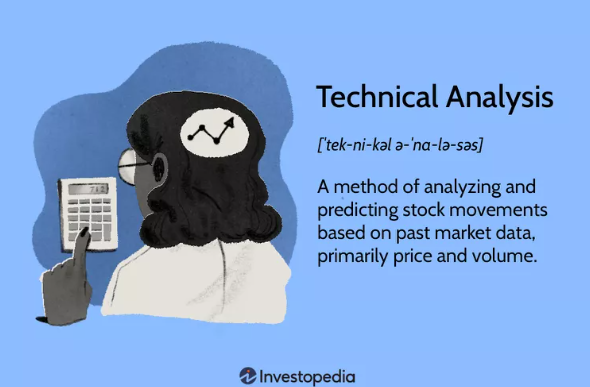
Image Source: Investopedia
Trading and investing have evolved rapidly, especially with technological advancements reshaping how markets operate. By year, markets have become more accessible but also more volatile. Algorithmic trading, real-time data streams, and global connectivity mean prices react faster than ever.
In this fast-paced environment, relying purely on news or fundamentals is insufficient. Technical analysis becomes an indispensable tool to cut through noise, spot emerging trends, and manage risk. It empowers traders whether day traders, swing traders, or long-term investors to respond to market shifts with a grounded strategy rather than emotion-driven guesses.
Moreover, technical analysis adapts well across asset classes. Whether you’re exploring stocks, cryptocurrencies, commodities, or forex, the principles remain consistent. The strategies you develop today will serve as a versatile toolkit for navigating diverse markets in year and beyond.
The Journey Begins: Building a Technical Mindset.
Many beginners make the mistake of rushing to learn “indicators” or “systems” before truly understanding the mindset behind technical analysis. But the real skill lies in cultivating patience, discipline, and emotional resilience.
Learning to “read the market’s mood” takes practice. Early on, you’ll encounter charts that look like chaotic scribbles. It’s natural to feel frustrated or confused. The key is to slow down and observe without the pressure to act immediately.
Consider this your apprenticeship phase, where you’re learning to listen to the market’s story. Journaling your observations, reflecting on your emotional reactions, and reviewing past trades even hypothetical ones builds the foundation for intuition.
A trader’s mindset is also about embracing uncertainty. No strategy guarantees success every time. Losses are part of the journey, and handling them without panic is a hallmark of a mature technical analyst.
True growth begins when we step beyond comfort and confront uncertainty with courage. The most profound changes often come disguised as challenges that shake our foundations. Instead of fearing these moments, we should welcome them as invitations to evolve. Growth is messy and slow, filled with doubts and failures, yet it’s within this struggle that we discover our real strength, clarity, and purpose. Every day holds a chance to become better than who we were yesterday.
The Essential Tools of Technical Analysis.
As you embark on your year trading journey, a few fundamental tools become your compass. These are not just fancy features on your trading platform; they are windows into market behavior.
Charts are your canvas. Most beginners start with candlestick charts, which provide more visual depth than simple line charts. Each candle tells a story of opening, closing, highs, and lows within a specific timeframe.
Volume data adds texture to the price story. Volume reveals how much interest there is behind a price move. A rising price on increasing volume suggests strength, while price moves on low volume may be suspect.
Trendlines are your guideposts. Drawing lines that connect swing highs or lows helps identify the direction of the market. Are prices climbing steadily? Or are they trapped in a sideways range? Trendlines visually highlight these conditions.
Beyond these basics, you’ll encounter indicators mathematical calculations based on price and volume. Popular ones include Moving Averages, RSI (Relative Strength Index), and MACD (Moving Average Convergence Divergence). While these can seem intimidating initially, they become invaluable once you understand their context and limitations.
Navigating Trends: The Heartbeat of Markets.
Markets don’t move randomly; they travel in trends. Recognizing whether you’re in an uptrend, downtrend, or sideways market is fundamental to any technical strategy.
An uptrend is characterized by higher highs and higher lows. It’s like walking uphill, where the momentum pushes prices upward. Conversely, a downtrend shows lower highs and lower lows, indicating sellers are in control.
But the most challenging market condition is a sideways or ranging market. Here, prices move within a horizontal band, reflecting indecision. Many beginners make the error of trying to “pick a direction” in such phases, often resulting in losses.
Understanding the trend helps you align your trades with the market’s natural flow. Trying to swim against a strong trend can be dangerous. Instead, learning to enter on pullbacks within a trend or waiting for trend reversals with confirmation is a mark of skillful trading.
Happiness is not a distant goal to chase but a state cultivated in everyday moments. It thrives in gratitude, presence, and the simple joys often overlooked amid life’s chaos. When we pause to appreciate what we have instead of fixating on what’s missing, we unlock a profound peace that no external achievement can provide. True happiness blooms from within nurtured by kindness, self-compassion, and the meaningful connections we foster with others.
Emotional Wisdom Embedded in Price Patterns.
Candlestick patterns, chart formations, and price action are more than technical tools they are emotional snapshots. For example, a “hammer” candle after a downtrend often reflects a market hesitating to continue lower, signaling potential reversal due to emerging buying pressure.
Similarly, formations like “head and shoulders” or “double tops” tell stories of exhaustion and battle between buyers and sellers. Rather than memorizing these patterns mechanically, try to visualize the underlying emotions.
Imagine yourself in the crowd of traders making those decisions. Why would someone sell here? Why does a breakout cause sudden buying frenzy? This empathetic approach deepens your connection with the charts and makes your analysis richer.
Risk Management: The Unsung Hero of Technical Analysis.
No discussion about strategies is complete without addressing risk management. Many beginners focus heavily on finding “perfect entry points” but neglect how to protect their capital.
In year’s fast-moving markets, managing risk is your lifeline. Technical analysis helps define where to place stop-loss orders the price point that invalidates your trade idea. This creates a clear exit plan and limits losses when the market doesn’t behave as expected.
Position sizing is another crucial aspect. It’s about adjusting how much capital you risk on each trade to survive inevitable losing streaks. This discipline keeps your trading sustainable and psychologically manageable.
Remember, no strategy wins all the time. Your goal is consistent, controlled growth, not gambling for quick wins.
Creativity is a quiet rebellion against the ordinary, an act of bravery where we let our authentic voice be heard. It thrives in curiosity and vulnerability, where mistakes become experiments and doubts fuel exploration. The creative journey is not about perfection but about expression, connection, and growth. By embracing imperfection and uncertainty, we open doors to innovation and self discovery, transforming our unique ideas into lasting impact.
Combining Multiple Technical Strategies for Robust Trading.
By now, you may be wondering if relying on one indicator or pattern is enough. The truth is, successful traders use a combination of methods to confirm signals and build confidence.
For example, a moving average crossover (where a short-term average crosses above a long-term average) might suggest a bullish trend. But confirmation from volume increasing or an RSI bouncing from oversold territory strengthens the trade idea.
In year, with more data and tools available, integrating multiple strategies thoughtfully is key. Avoid “indicator overload” too many signals can confuse you. Instead, develop a personalized system that fits your style and risk tolerance.
The Role of Technology and AI in Modern Technical Analysis.
While the human element remains paramount, trading in year is deeply intertwined with technology. AI-driven tools, algorithmic scanners, and real-time alerts offer traders a powerful edge.
However, beginners should approach these tools as assistants, not replacements for their own analysis. Technology can help spot setups faster, backtest strategies, and manage trades efficiently, but understanding the “why” behind signals keeps you in control.
Developing your own technical insight alongside technological aids creates a balanced approach, blending emotional intelligence with data precision.
Cultivating Patience and Continuous Learning.
Perhaps the most understated aspect of mastering technical analysis is patience. Market conditions will test your resolve. You will miss trades, experience losses, and sometimes question your ability.
It’s crucial to view this process as a marathon, not a sprint. Each trade is a lesson, and each day you spend observing charts builds your expertise.
Continuous learning is also vital. Markets evolve, and so should your strategies. Journaling your trades, reviewing outcomes, and adapting keeps your edge sharp.
Seek out communities, mentors, and credible educational resources to enrich your journey. Trading can be solitary, but wisdom grows faster when shared.
Leadership is not defined by titles or power but by the ability to inspire trust, empathy, and vision in others. A true leader listens deeply, acts with integrity, and embraces the responsibility to uplift those around them. Leadership requires humility recognizing that every success is a collective achievement. It’s about guiding with compassion through uncertainty, fostering collaboration, and empowering others to shine alongside you.
Final Thoughts:
Starting your technical analysis journey in year means stepping into a dynamic, challenging, yet rewarding world. The strategies you develop will be shaped not just by charts and indicators but by your mindset, discipline, and emotional intelligence.
Remember, there is no “one-size-fits-all” formula. Technical analysis is as much art as it is science. Your path will be unique marked by your learning style, risk appetite, and goals.
As you wrap up this beginner’s journey into technical analysis strategies for 2025, remember that mastering these tools is less about quick wins and more about developing a deep understanding of how markets speak through price.
It’s a journey filled with learning, patience, and sometimes frustration—but also with rewarding moments of clarity when the patterns finally make sense. Trust yourself to grow steadily, embrace the process, and keep your curiosity alive.
The market’s rhythm may seem complex now, but with time, it will become a language you fluently understand. Here’s to your success in navigating the exciting markets of 2025!
Embrace the complexity, stay curious, and most importantly, trust the process. Over time, the charts will become less intimidating and more like a trusted map guiding you through the vast markets.
May your 2025 trading journey be insightful, disciplined, and fulfilling.